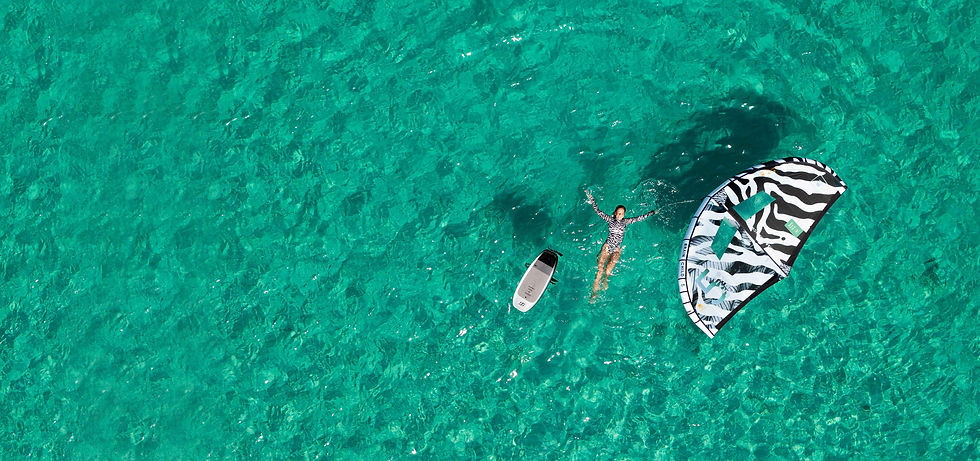

Future Production
At BRAINCHILD, we have set ourselves ambitious goals.
We consider our mission essential for the innovation-driven development of water sports equipment and our environment.
We have set out to become the most advanced and largest kite and wing OEM production facility.
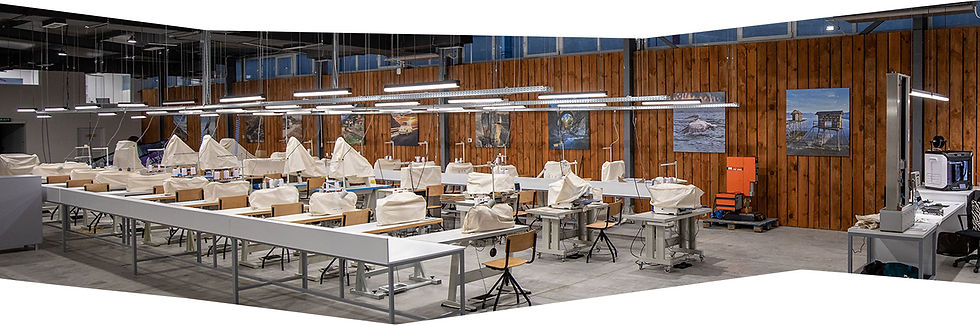

Laboratory & Manufactory
Consisting of the BRAINCHILD Laboratory and the BRAINCHILD Manufactory, we operate two competence centres close to each other.
The Laboratory is where new manufacturing techniques are developed, advanced materials are researched, and quality assurance is carried out. This is where our creative centre is located - a high-performance ideas hub. We can produce ready-to-use prototypes, and small series runs in a very short time.
With the BRAINCHILD Manufactory, we are setting up our own factory for series production for our OEM customers.



We set standards
We have undertaken the task of sustainably developing and producing the most innovative kite- and wingfoil equipment in the heart of Europe.
To achieve this, BRAINCHILD uses state-of-the-art and, at the same time, environmentally friendly production technologies as well as new materials.
As a result, products from our manufacturing facility are revolutionary in terms of performance and set standards through their resource-saving production.
Innovation and sustainability are the two pillars on which BRAINCHILD Production is built.

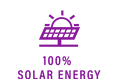




EVERY DETAIL COUNTS
Innovative & individual
As an OEM manufacturer, we produce kite- and wing equipment for the future of water sports brands all over the world. BRAINCHILD founder Ralf Grösel has developed a modular system in which every component has been carefully considered.
Thanks to new production techniques and materials, BRAINCHILD products offer revolutionary
performance and set new standards for eco-friendly manufacturing.
Furthermore, thanks to our production technologies, we can offer our customers an extremely high degree of customisation with unrivalled quality - whether it‘s graphically complex designs or pioneering construction solutions.
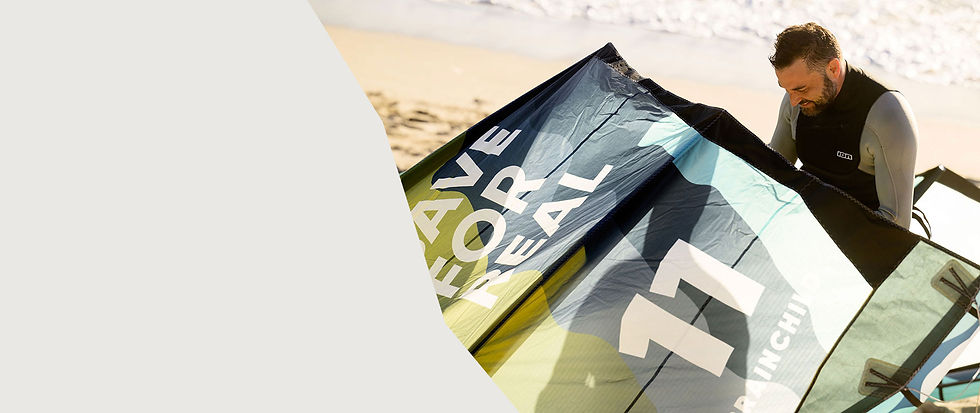
„Wind driven sports are my passion.
After 22 years within this industry,
it,s time to reimagine.“
Ralf Grösel / CEO Brainchild Production

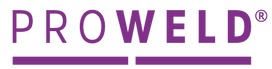
Unique & Revolutionary Process Technology
With PROWELD, segments are ultrasonically welded together seamlessly at one point and then glued on the back to increase the structural rigidity of the joint.
The big advantages of the PROWELD method:
-
The diagonal stiffness of the Dacron is much higher than with conventional stitching.
-
This leads to an increase in the overall stiffness of the product.
-
Saves weight as less material is required for this type of seam.

-15 %
weight reduction compared to a conventional seam construction.

+ 25 %
increased torsional stiffness
of the supporting structure.

Digital Printing will enable lot sizes of "one"
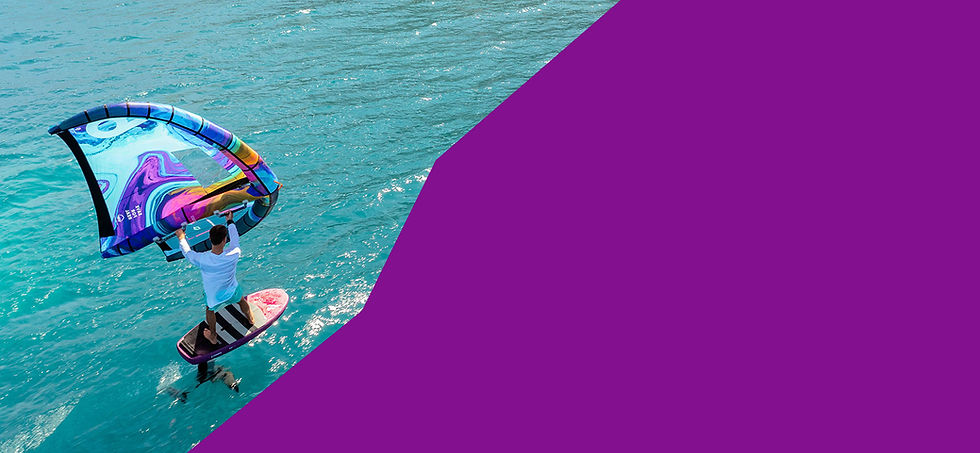
A revolution for the kite and wing industry
No limitation in design and quantities any more
Eco-friendly and simplifying stock management
to ONE base color
Possibility of web-to-print and lot sizes of “ONE“*
enabling customization in the regular mass

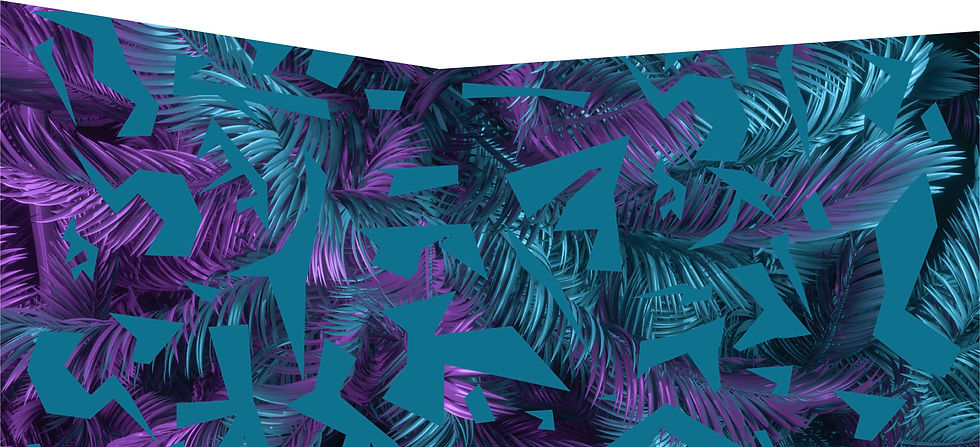
SAVE
FOR
REAL
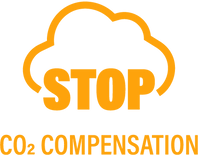

FOLLOW US